Contact resistance
With these two contacting plates, the formula used previously supposes
they are in perfect contact, which would be the case
if the two surfaces which make the interface between the two plates
were perfectly flat and smooth.
Once again, reality is cruel but here we can't neglect it ! Surfaces
in contact are not smooth nor flat, they always have a rough
pattern which looks like this:

The effect of roughness is very important; in general the real
surface contact area is never higher than 2% of the
interface surface area, yes 2%!!! This leaves enough places for
micro-cavities filled with air, which has a very
bad thermal conductivity ( see the table of conductivities at the beginning ).
All this thickness ( 0.5 - 60 mm for flat
surfaces ) consisting of roughness and air gaps form a thin layer
which will less conduct heat, this translates into contact resistance
Rc
which will depend of :
- the form and the distribution of roughness ( i.e. surface finish
)
- the thermal conductivity of the air -or of the material- which
fills the gaps ( higher is better )
- the hardness of materials and the contact pressure between the
two plates ( softer materials and higher pressure allow to" crush
" more easily roughness and thus offer a greater real surface
contact area )
- the apparent interface surface area ( a larger interface offers
less resistance )
This resistance is added to the thermal circuit :
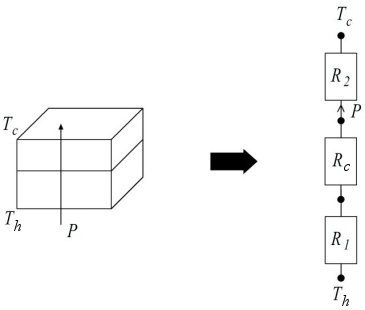
The means to reduce the contact resistance are well known :
- lapping to obtain the smoothest and moreover the
flattest surfaces' quality as the temperature can be reduced up
to 4°C ( thanks to Bill
Adams )
- replacing the air cavities by a substance of better thermal
conductivity like thermal paste
- increasing the mounting pressure by tightening
the assembly as much as possible ( but in practice within the
range of what a cpu supports ! ).
|